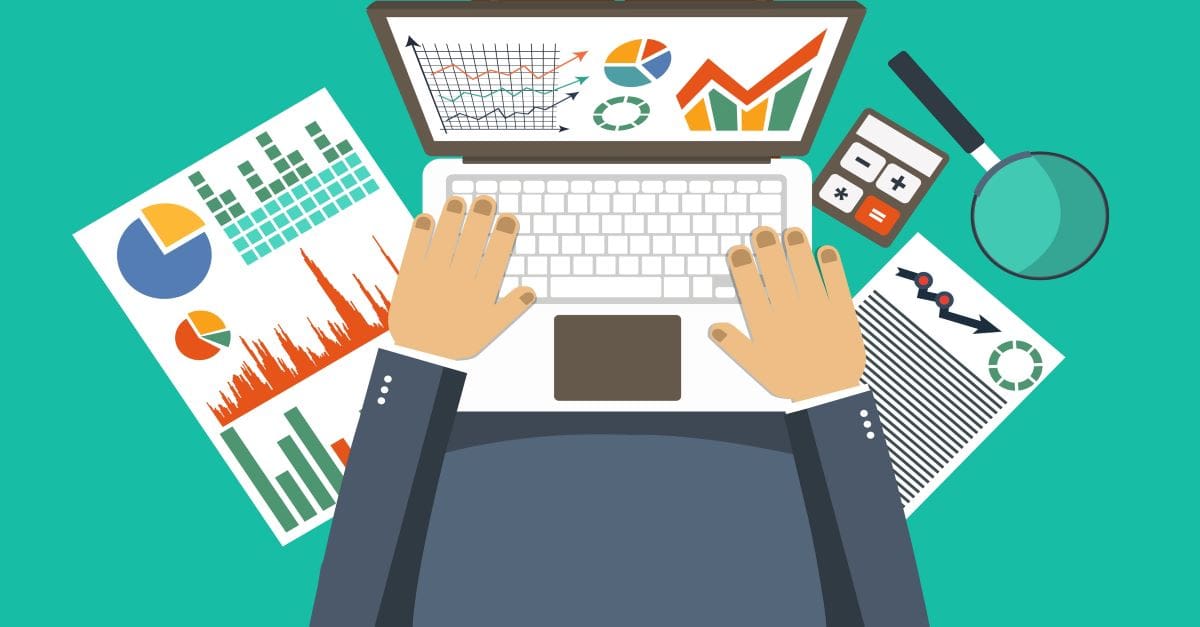
Laboratory reporting is more than just data entry—it’s the cornerstone of decision-making in modern labs. Whether you’re delivering patient results, regulatory reports, or internal performance metrics, your reporting process must be fast, accurate, and audit-ready. This article explores how to optimize laboratory reporting using the latest tools, workflows, and strategies to meet the demands of today’s data-driven scientific environments.
What Is Laboratory Reporting?
Laboratory reporting is the process of collecting, organizing, and presenting laboratory data in a meaningful format for stakeholders. Reports may include test results, quality control summaries, chain-of-custody records, compliance metrics, or operational KPIs. Effective laboratory reporting ensures the right information reaches the right people—on time and in the correct format.
Why Laboratory Reporting Matters
Accurate and timely lab reports are critical for:
- Clinical Decision-Making: Ensuring doctors and healthcare providers receive reliable results
- Regulatory Compliance: Meeting the standards of bodies like the FDA, EPA, or ISO
- Operational Visibility: Enabling lab managers to track performance and resource use
- Customer Satisfaction: Providing transparent and timely updates to clients and stakeholders
Common Challenges in Laboratory Reporting
Despite its importance, many labs struggle with inefficient reporting workflows. Common challenges include:
- Manual data entry that introduces errors and delays
- Lack of standard templates or inconsistent formatting
- Limited visibility across departments or systems
- Difficulty meeting complex compliance and audit requirements
These obstacles can lead to reporting delays, failed audits, and reputational damage—making optimization a top priority.
How to Improve Laboratory Reporting
1. Automate Data Capture and Report Generation
Automated laboratory systems, including instruments and LIMS platforms, can feed data directly into reports without manual transcription. This reduces errors, saves time, and ensures that reports reflect real-time data.
2. Standardize Templates and Output Formats
Using standardized templates improves clarity and consistency across all reports. Whether you’re reporting to clinicians, clients, or regulators, tailored templates reduce misinterpretation and speed up review.
3. Integrate Your LIMS for Centralized Reporting
A Laboratory Information Management System (LIMS) serves as the central hub for lab data, making it ideal for managing and generating reports. A modern LIMS allows you to create custom reports based on user roles, workflows, and compliance needs—all while maintaining an audit trail.
4. Use Dashboards for Real-Time Visibility
Dashboards allow lab staff and managers to view key performance indicators (KPIs), test status, and turnaround times at a glance. By visualizing data trends, labs can proactively manage workloads and identify bottlenecks.
5. Implement Role-Based Access and Approvals
Not every user should see or edit every report. Role-based access and digital sign-offs ensure that only authorized personnel can generate or approve official documents, which is critical for both security and compliance.
The Role of Compliance in Laboratory Reporting
Laboratory reporting must align with strict regulatory frameworks depending on your industry. For example:
- CLIA and HIPAA in clinical labs
- FDA 21 CFR Part 11 for electronic records and signatures
- ISO/IEC 17025 for testing and calibration labs
- EPA and state regulations for environmental testing
Your reporting tools should support these standards with features like secure login, audit trails, version control, and electronic signatures.
How the LabLynx LIMS Suite Optimizes Laboratory Reporting
The LabLynx LIMS Suite transforms how labs handle reporting by integrating advanced features into a unified platform. With configurable templates, automated workflows, and real-time dashboards, our LIMS allows labs to generate detailed, compliant reports with minimal effort.
Whether you need to deliver client-ready PDFs, internal metrics, or audit reports, LabLynx makes reporting fast, accurate, and easy to manage.
Schedule a demo to see how LabLynx can elevate your lab’s reporting capabilities with a fully integrated solution.
Conclusion: Better Reporting, Better Outcomes
Optimizing laboratory reporting isn’t just about faster turnaround—it’s about increasing the integrity and impact of the work your lab performs. By embracing automation, standardization, and modern lab software like the LabLynx LIMS Suite, your lab can ensure reports are accurate, timely, and fully compliant. In today’s data-driven landscape, better reporting leads to better science—and better outcomes for everyone involved.
Accelerate Your Lab's Success & Experience LabLynx
"*" indicates required fields
Explore the LabLynx Suites
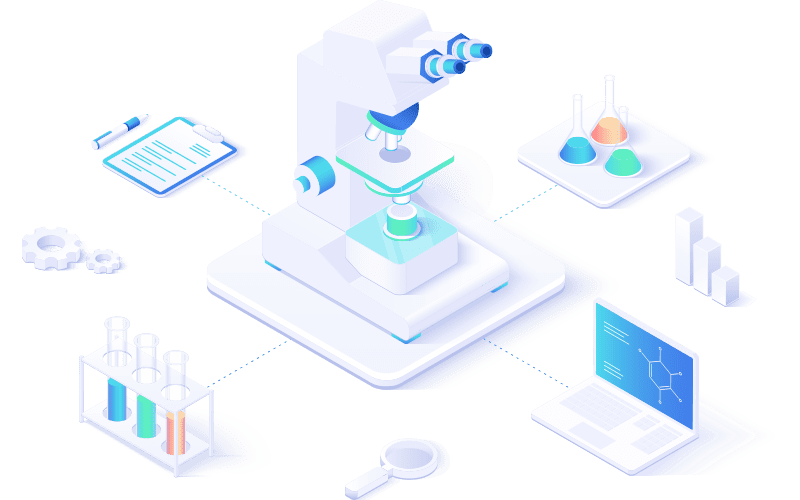
LIMS Suite
Seamless Sample and Workflow Management
The LabLynx LIMS Suite empowers laboratories with the tools needed to manage samples, workflows, compliance, and more in one centralized system. It’s the backbone for labs seeking efficient, reliable, and scalable management solutions.
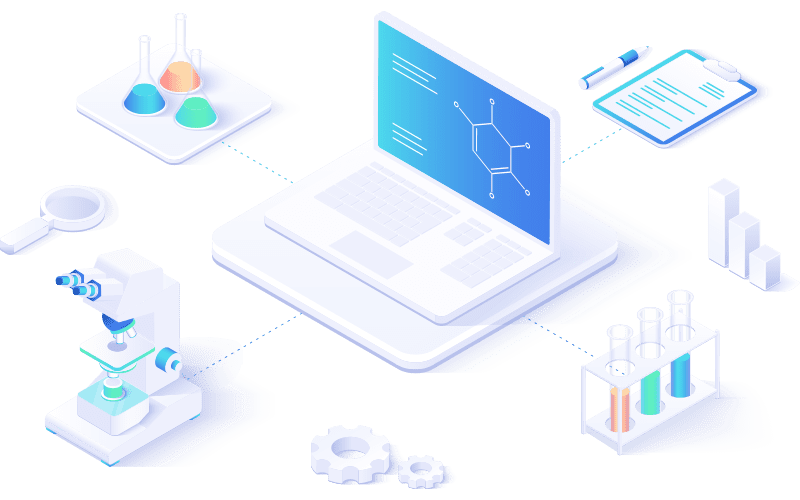
ELN Suite
The LabLynx ELN Suite offers a modern approach to managing lab data and experiments. With its secure, intuitive platform, your team can record, store, and collaborate effortlessly, supporting innovation every step of the way.
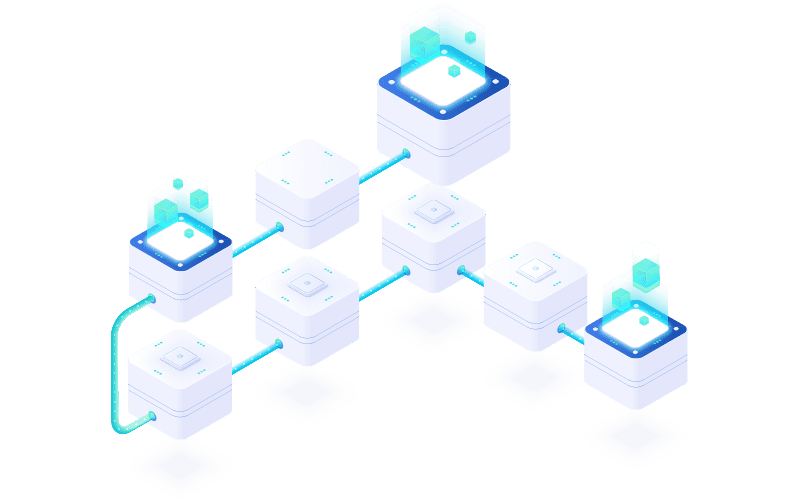
Lab Automation
Automate for Efficiency and Growth
Streamline operations and boost productivity with the LabLynx Lab Automation Suite. Designed for labs ready to embrace advanced automation, this suite integrates systems, instruments, and workflows to deliver efficiency at scale.