Advance Academic Research with a Smarter Electronic Lab Notebook
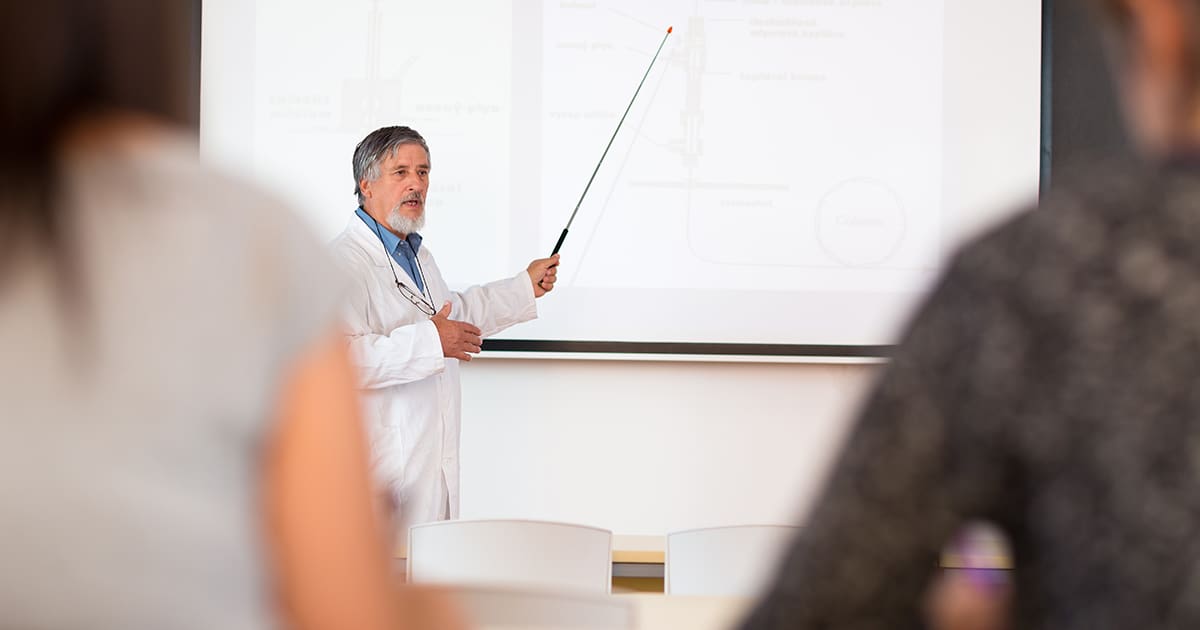
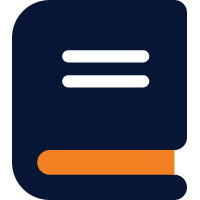
Academic Research ELN: Streamline Data, Enhance Collaboration, and Accelerate Discoveries
Academic research labs handle vast amounts of data, requiring a seamless, secure, and efficient solution for documentation and collaboration. LabLynx Academic Research ELN is designed to support universities, institutions, and research teams with an intuitive platform that simplifies experiment tracking, ensures data integrity, and enhances workflow efficiency. With powerful tools for version control, structured templates, and real-time collaboration, researchers can focus on groundbreaking discoveries without the burden of manual data management.
LabLynx ELN provides a flexible, cloud-based solution that adapts to the unique needs of academic research labs, ensuring compliance with funding and institutional guidelines. Whether managing multi-disciplinary projects, securing intellectual property, or integrating with existing lab systems, our ELN keeps research organized, accessible, and reproducible. Elevate your research capabilities with a platform that empowers innovation and keeps your lab at the forefront of scientific advancement.
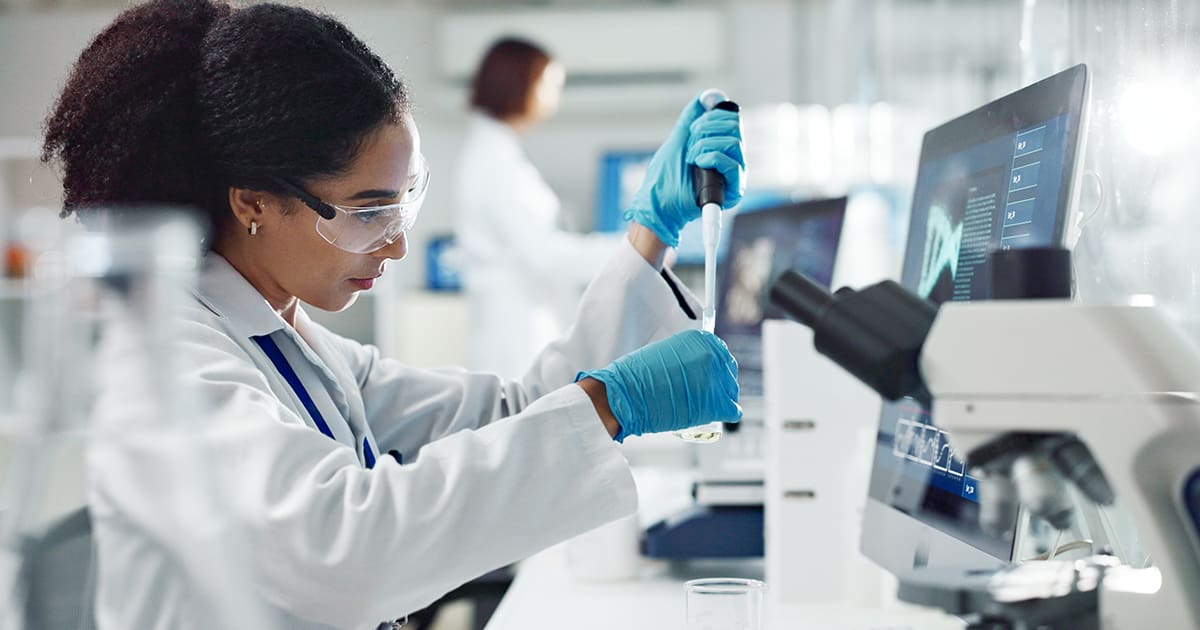
Don’t let a one-size-fits-all solution hold your lab back—discover how our customizable ELN can transform your operations.
Essential LabLynx ELN Features for Academic Research Labs
Academic research labs require an intuitive, flexible, and secure digital solution to streamline data management, enhance collaboration, and ensure research integrity. LabLynx ELN is designed to support universities, research institutions, and collaborative teams with advanced tools for documentation, version control, and compliance. Explore the key features that make LabLynx ELN the ideal solution for academic research labs.
Efficient Research Data Management
Structured Experiment Documentation
LabLynx ELN provides customizable templates for experiments, ensuring consistent, organized, and reproducible research documentation across academic studies.
Centralized Research Data Storage
Securely store and manage all research data, notes, and protocols in one cloud-based repository, eliminating scattered files and ensuring long-term data accessibility.
Version Control & Audit Trails
Automatically track changes, maintain version history, and ensure full research integrity and compliance with built-in audit trails and digital timestamps.
Seamless Collaboration & Multi-User Access
Real-Time Collaboration & Sharing
Facilitate teamwork with multi-user access, shared workspaces, and role-based permissions, enabling researchers to work together efficiently across institutions.
Integration with Institutional Systems
LabLynx ELN seamlessly connects with LIMS, lab instruments, and third-party research tools, ensuring smooth workflows and interoperability across platforms.
Cloud Accessibility for Remote Research
Access research data anytime, anywhere with secure cloud-based hosting, allowing academic teams to collaborate effectively regardless of location.
Compliance, Security & Intellectual Property Protection
Regulatory & Funding Compliance
Ensure adherence to institutional, government, and funding body guidelines, including NIH, NSF, and IRB protocols, with built-in compliance tools.
Robust Data Security & Encryption
LabLynx ELN protects sensitive research with enterprise-grade encryption, role-based access controls, and automated backups, ensuring data confidentiality.
Intellectual Property & Research Rights Protection
Maintain control over research findings with secure authorship tracking and time-stamped records, ensuring proper attribution and IP security.
Customization & Scalability for Academic Research
Flexible Workflows & Configurable Templates
Customize research workflows and experiment templates to match the specific needs of various academic disciplines and research methodologies.
Scalable for Growing Research Projects
LabLynx ELN grows with your institution, supporting multiple users, expanding research teams, and integrating new technologies as your research evolves.
Grant & Project Management Tools
Track research grants, funding allocations, and project timelines with built-in tools that help manage academic budgets and reporting requirements.
Discover How LabLynx Boosts Your Academic Research Lab’s Performance and Efficiency
"*" indicates required fields
LabLynx ELN Suite for Academic Research Labs
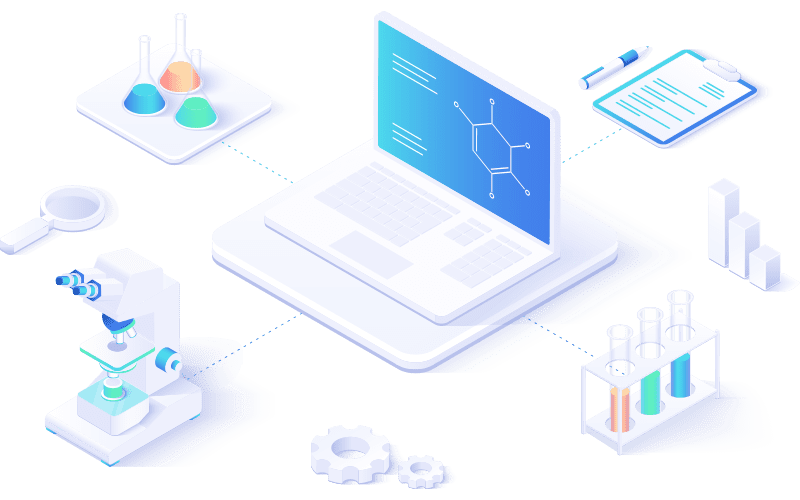