Optimize Automotive Lab Efficiency with Custom Lab Management Solutions
LabLynx empowers automotive manufacturing labs with digital tools to streamline testing, eliminate manual errors, and improve decision-making. By replacing outdated systems with customized automation, labs enhance report accuracy, improve turnaround times, and ensure quality control across every shift and production line.
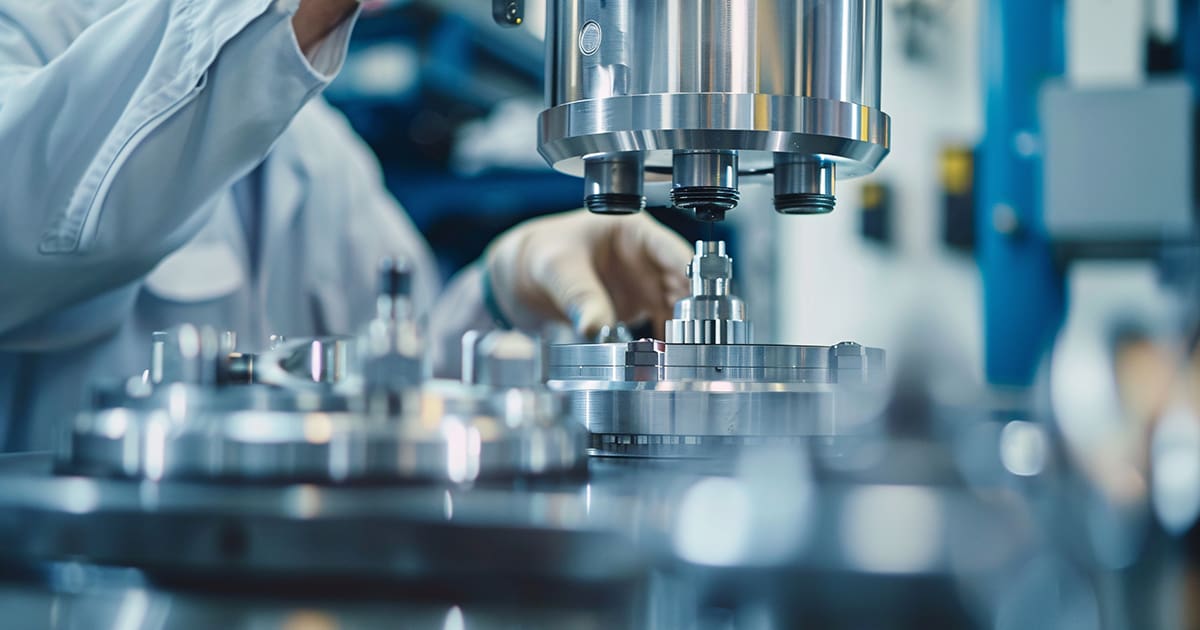
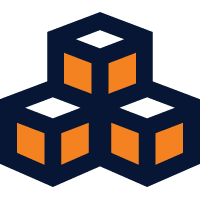
Manual Lab Systems Delayed Workflows and Risked Data Integrity
Before implementing LabLynx, a high-volume lab supporting an automotive component manufacturer relied on manual processes, paper records, and spreadsheets to manage its rigorous testing operations. The lab examined hundreds of magnet samples daily to ensure dimensional accuracy and magnetic performance, yet approvals and reports were generated by hand, making it difficult to analyze trends, trace data, or respond to urgent requests. This approach not only slowed productivity but also introduced significant risk for human error and compliance challenges.
A broader global initiative to digitize lab operations prompted the need for change. Lab leaders identified critical gaps in security, access control, and instrument integration that could no longer be managed with their existing system. They needed a solution that would streamline approvals, automate data capture from testing equipment, and provide real-time access to lab data—all while supporting 24/7 operations and complex reporting needs.
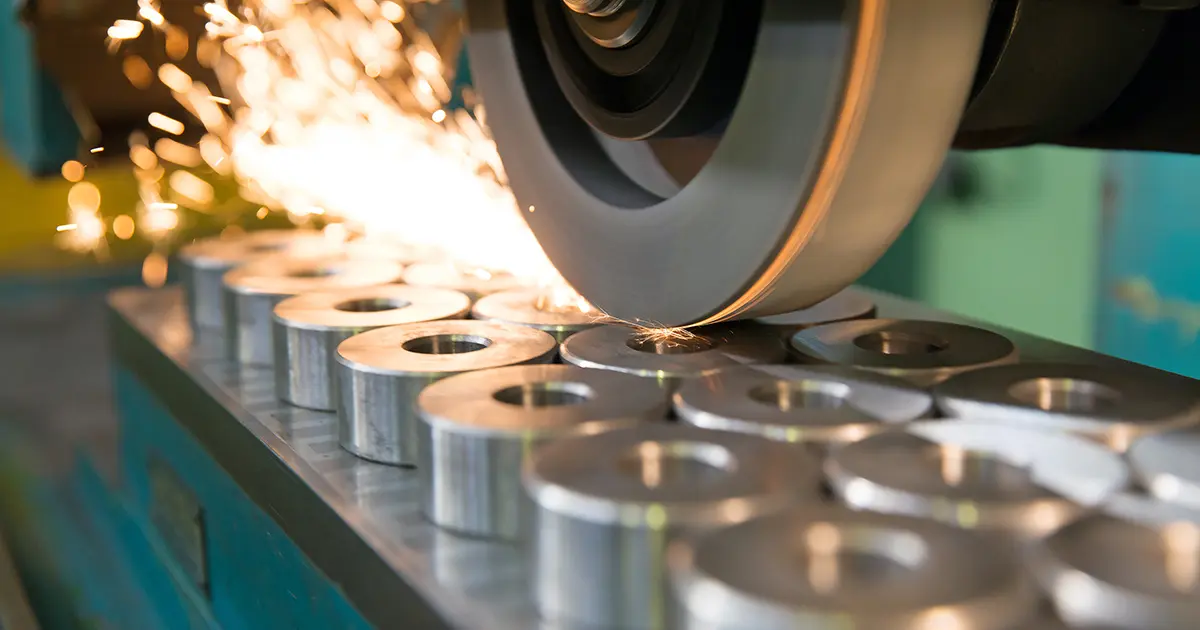
LabLynx Delivered Configurable Automation That Improved Speed, Accuracy, and Access
To align with the company’s modernization initiative, the lab selected LabLynx as its LIMS partner due to the platform’s flexibility, customization, and responsiveness. Implementation began with a site visit to document existing workflows, terminology, and instrumentation needs. LabLynx engineers then worked closely with the lab team and international management to configure a solution that matched their exact specifications.
The customized LabLynx LIMS eliminated paper reporting and automated the transfer of data from testing instruments directly into the system, significantly reducing the risk of transcription errors. Secure access controls allowed only authorized team members to approve reports or view sensitive data. For lab managers working around the clock, the remote access feature meant they could review reports or respond to customer requests anytime, anywhere.
Even with ongoing changes requested by leadership during the project, LabLynx remained flexible and efficient. Within months, the lab had a fully functioning LIMS that dramatically improved operational efficiency by an estimated 25 percent. The system also enhanced traceability, enabling faster and more accurate responses to customer quality questions and audit requirements.
With LabLynx, the lab met its goals of modernizing data collection, improving security, and empowering lab staff to work smarter—not harder.
Don’t let a one-size-fits-all system limit your lab—discover how our customizable solutions can streamline operations and support your unique workflows.
Smarter Lab Operations with LabLynx: Key Advantages and Outcomes
This automotive component testing lab achieved significant improvements in efficiency, accuracy, and security by replacing outdated systems with LabLynx LIMS. With automated data collection, role-based access, and real-time reporting, the lab reduced human error, ensured regulatory compliance, and responded to customer needs with speed and confidence.
Key Features That Transformed Lab Operations
Automated Instrument Data Capture
The lab eliminated manual data entry by integrating LabLynx with critical test instruments, ensuring data accuracy and minimizing the risk of human error. This direct data flow helped streamline workflows and increase overall throughput.
Custom Access Controls and Approvals
Lab managers used configurable access settings to restrict data visibility and enforce approval workflows, ensuring sensitive reports were only accessible to authorized users. This feature improved security and audit readiness.
Remote System Access for 24/7 Operations
With around-the-clock testing schedules, managers could securely access the LIMS remotely to review data or send customer reports after hours. This flexibility boosted responsiveness and eliminated bottlenecks.
Top Reasons This Lab Chose LabLynx
Highly Customizable System Architecture
LabLynx offered the ability to build every field, workflow, and approval process around the lab’s exact needs. This configurability allowed the team to replicate their processes digitally without compromising quality.
Superior Support and Responsiveness
Throughout implementation, LabLynx engineers adapted quickly to changing requirements and provided consistent support, including global coordination with international leadership teams.
Cost-Effective, All-in-One Solution
Compared to other LIMS platforms, LabLynx delivered all required functionality—including instrument integration and role-based security—at a lower total cost, with no need to purchase extra modules.
Discover How LabLynx Can Improve Your Laboratory
"*" indicates required fields