Optimize Medical Device Lab Efficiency with a Unified Digital Lab Management System
LabLynx empowers medical device testing labs with configurable digital tools to meet regulatory requirements, eliminate paperwork, and improve cross-lab collaboration. With LabLynx, labs can streamline workflows, reduce audit risk, and increase accuracy while scaling lab operations globally across multiple lab types and geographies.
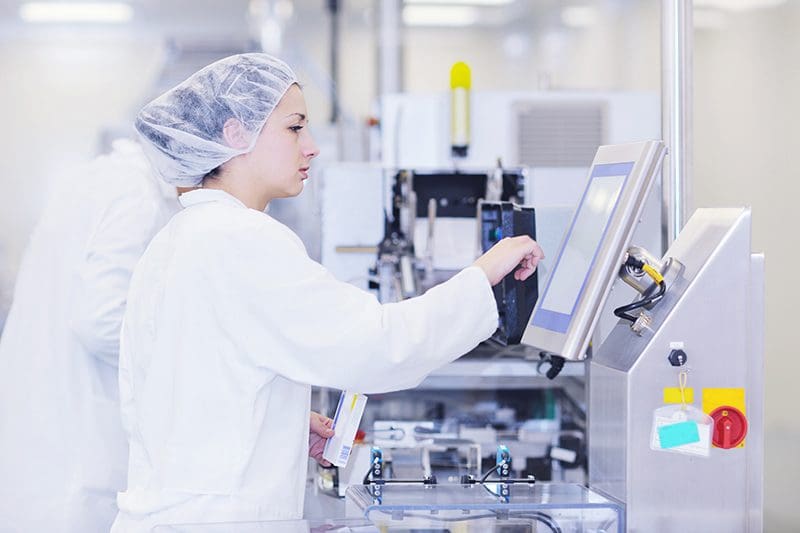

Legacy Systems and Rising Regulatory Demands Pushed This Global Manufacturer to Find a Smarter LIMS Solution
A major medical device company operating labs across the US, Europe, and South America found its outdated testing system increasingly unsustainable. Compliance workflows were difficult to enforce, new team members often missed critical steps, and tracking lab activities was fragmented across digital and paper systems.
As a highly regulated business, the stakes were high. Each mistake could trigger an investigation and require time-consuming corrective action. The company knew it needed a laboratory information management system (LIMS) that could enforce workflow consistency, maintain audit trails, and integrate smoothly across multiple lab types, including microbiology, chemistry, physical testing, and pharmaceutical labs.
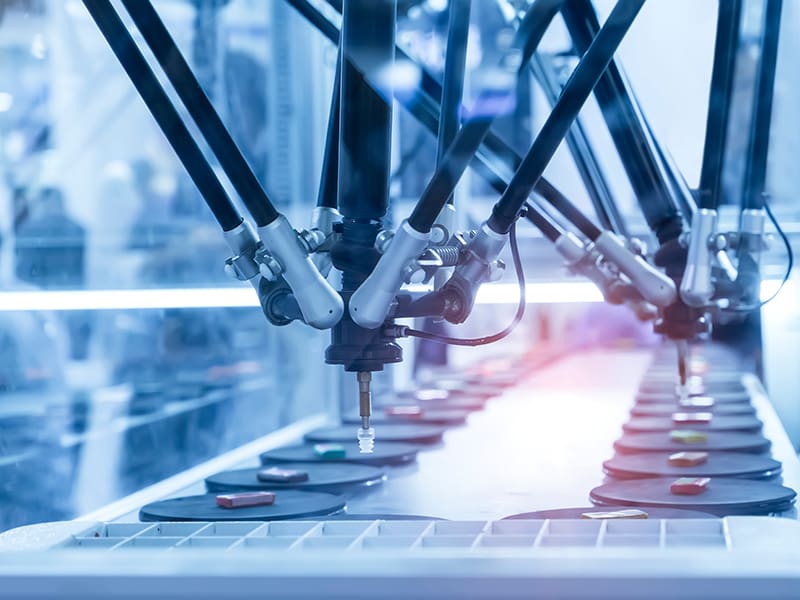
A Flexible and Fully Configured LIMS Platform Transformed Lab Performance Across the Enterprise
The company implemented LabLynx LIMS in its initial three labs to centralize testing processes, improve traceability, and move away from paper tracking. These early successes created a ripple effect, leading to the adoption of LabLynx LIMS in five more labs through internal referrals and growing interest from other lab teams.
LabLynx LIMS allowed each lab to create specific workflows for their unique testing protocols, eliminating skipped steps and ensuring consistency. This capability was essential for both quality control and regulatory audits, where lab staff needed to document every piece of equipment, solution, and step used in the testing process. With built-in audit trails and structured workflows, the company significantly reduced audit findings and human error.
Another major win was LabLynx’s all-in-one platform. Competing LIMS systems required purchasing separate modules for inventory, instrumentation, or reporting. LabLynx offered everything in one package, including a customer portal, inventory tracking, and cloud hosting—all customizable to each lab’s specific needs. The system was scalable, supported instrument integration, and reduced manual tasks, allowing lab staff to focus on higher-value work.
Don’t let a one-size-fits-all system limit your lab—discover how our customizable solutions can streamline operations and support your unique workflows.
Smarter Lab Operations with LabLynx: Key Advantages and Outcomes
LabLynx provided this global manufacturer with a single, adaptable platform that supported compliance, streamlined operations, and replaced outdated systems. With faster implementation, improved efficiency, and strong support, the company expanded the platform into additional labs, reinforcing a culture of consistency and quality.
Key Features That Transformed Lab Operations
Standardized Workflows for Compliance
Each lab can configure its own testing workflows to ensure step-by-step adherence and eliminate omissions. This reduces non-conformance events and improves training consistency for new staff.
Integrated Audit Trails and Traceability
All data modifications are logged with user justifications, maintaining full transparency and compliance with regulatory expectations. Lab teams can quickly identify the root of any issue.
Instrument and Inventory Tracking
Built-in tracking capabilities allow labs to monitor solution expiration, equipment calibration, and sample chain of custody. The system ensures no testing step relies on outdated or unverified materials.
Top Reasons This Lab Chose LabLynx
All-in-One System Without Modular Costs
Unlike other vendors that required purchasing separate modules, LabLynx provided a complete lab management system with everything included—saving both time and budget.
Configurable for Multiple Lab Types
LabLynx was able to support different workflows for microbiology, chemistry, and pharmaceutical testing all within the same database. This flexibility simplified management across the enterprise.
Responsive Support and Transparent Pricing
LabLynx’s team was praised for being highly responsive and collaborative during implementation. Transparent pricing and shorter timelines helped fast-track adoption across more labs.
Discover How LabLynx Can Improve Your Laboratory
"*" indicates required fields