Advanced LIMS Implementation for Specialty Materials Lab Operations
A large specialty materials laboratory located in Rhode Island sought to modernize its lab operations and reinforce data integrity. Focused on producing engineered metal powders used in electronics, the lab faced rising demands for secure access controls and efficient batch tracking. LabLynx LIMS delivered a tailored digital solution that addressed critical workflow challenges, improved compliance, and supported seamless integration with enterprise-level systems.
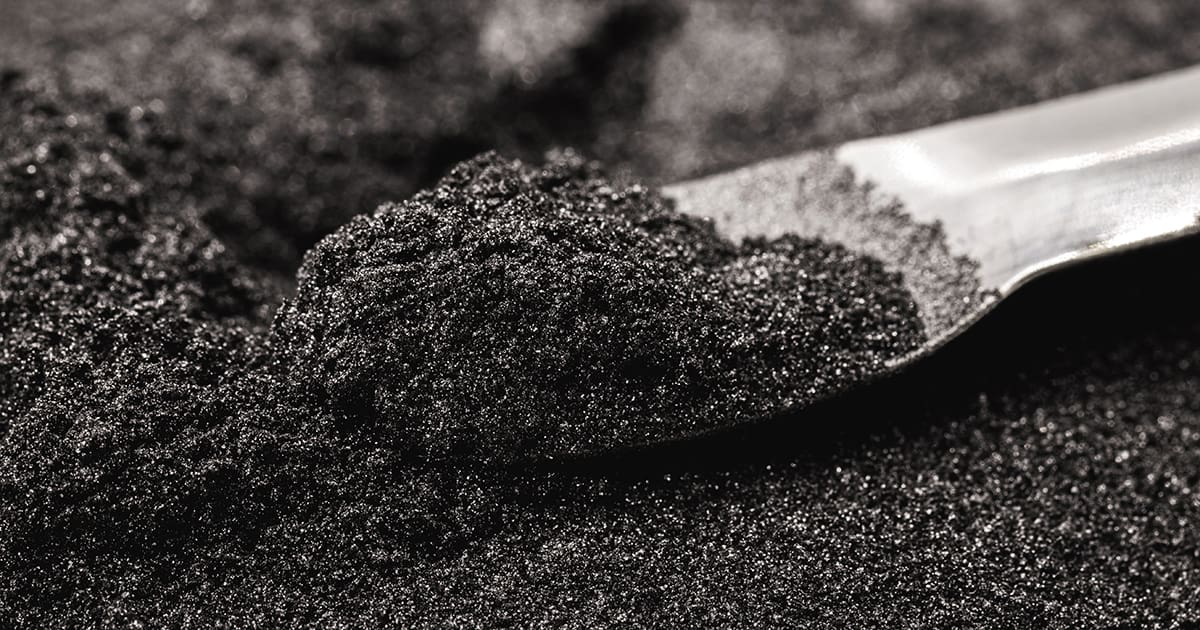
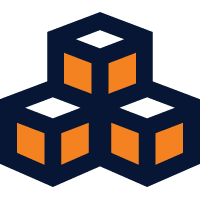
Outdated Systems Created Security Risks and Workflow Chaos
When the lab’s Microsoft Access database became obsolete and unsupported, the entire testing process became vulnerable. No login restrictions were in place, and anyone could alter sensitive testing data at any time. This lack of security made it difficult to maintain accuracy and consistency in reporting. The database was also linked to a sales order entry system, which compounded the risk, as data could be inadvertently overwritten or lost.
With up to 40 batches processed daily and various particle size and morphology tests conducted on each, the lab was overwhelmed with unstructured data and inefficient manual processes. The lab manager described spending over an hour each day sorting through logs and trying to identify issues with batch tracking and data discrepancies.
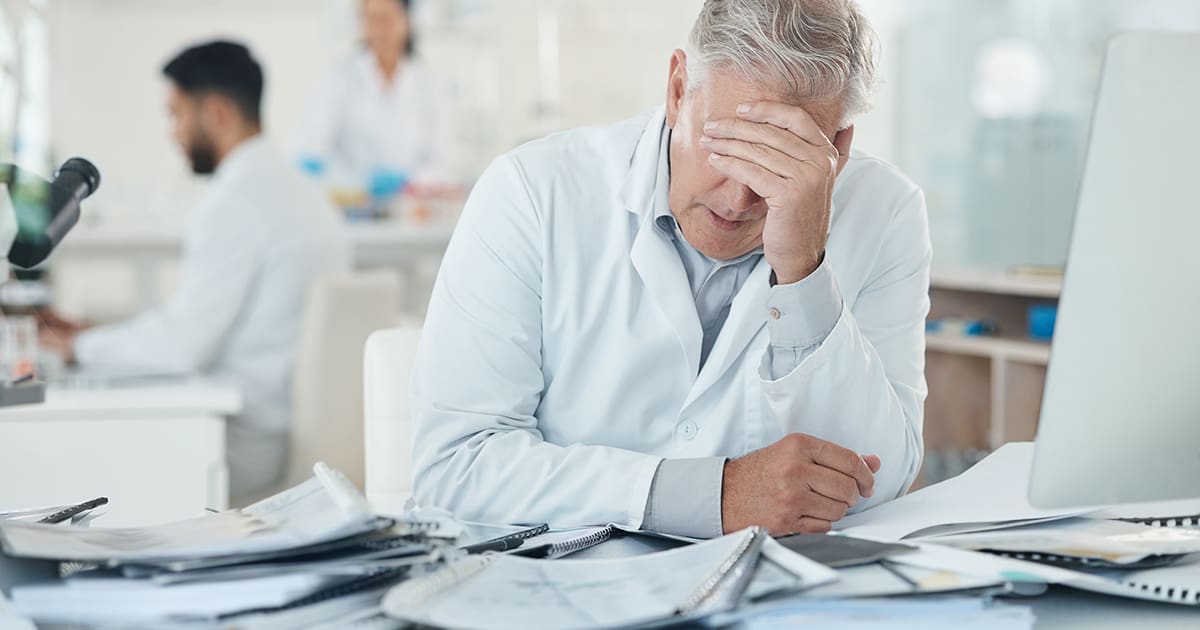
A Configurable and Supported Solution That Delivered Immediate Results
After evaluating four LIMS vendors, the lab selected LabLynx due to its willingness to customize and its ability to integrate directly with the company’s order entry system. Unlike rigid, out-of-the-box platforms, LabLynx offered the flexibility to tailor workflows and menu options based on how the lab actually operated. This customization was essential for a facility that managed large volumes of highly specialized materials and complex testing processes.
The implementation process moved quickly, taking approximately three months. A LabLynx applications engineer visited the lab in person to observe daily operations, engage with individual departments, and align the system to the lab’s exact requirements. This hands-on approach ensured that the final interface was intuitive and that each team had a workflow that matched its specific needs. LabLynx also created custom report formats and interfaces to support both internal processes and customer documentation.
To minimize internal IT burden, LabLynx hosted the LIMS database offsite and provided reliable, ongoing support. This was a critical factor for the lab, which had limited technical staff available to manage infrastructure. With LabLynx handling the hosting and maintenance, the team gained peace of mind knowing that issues could be resolved quickly—often within hours—rather than waiting on internal resources or dealing with prolonged downtime.
Don’t let a one-size-fits-all system limit your lab—discover how our customizable solutions can streamline operations and support your unique workflows.
Smarter Lab Operations with LabLynx: Key Advantages and Outcomes
LabLynx LIMS transformed a formerly chaotic lab into a structured, secure, and efficient operation. From improved traceability to responsive customer support, the lab continues to benefit from a flexible platform built to evolve with its needs.
Key Features That Transformed Lab Operations
Custom Access Controls
User roles and permissions ensure that only authorized staff can modify critical testing data. This dramatically reduces the risk of data tampering or error.
Integrated Order Entry Synchronization
The LIMS seamlessly communicates with the company’s order management system, reducing duplicate data entry and ensuring consistency across departments.
Automated Batch Number Generation
Batch numbers are now system-generated, eliminating reliance on paper logbooks and streamlining the tracking process for every manufactured material.
Top Reasons This Lab Chose LabLynx
Tailored Workflow Interfaces
LabLynx worked closely with staff to configure menus and workflows that matched exactly how the lab operates, reducing learning curves and improving adoption.
Remote Hosting and Maintenance
With LabLynx managing the system offsite, the lab avoids IT headaches and benefits from quick resolutions to any issues—often in hours, not weeks.
Responsive Customer Service
Whether it’s modifying a report or adding an ISO-9001 sticker, LabLynx’s ongoing support ensures the lab’s evolving needs are always met.
Discover How LabLynx Can Improve Your Laboratory
"*" indicates required fields