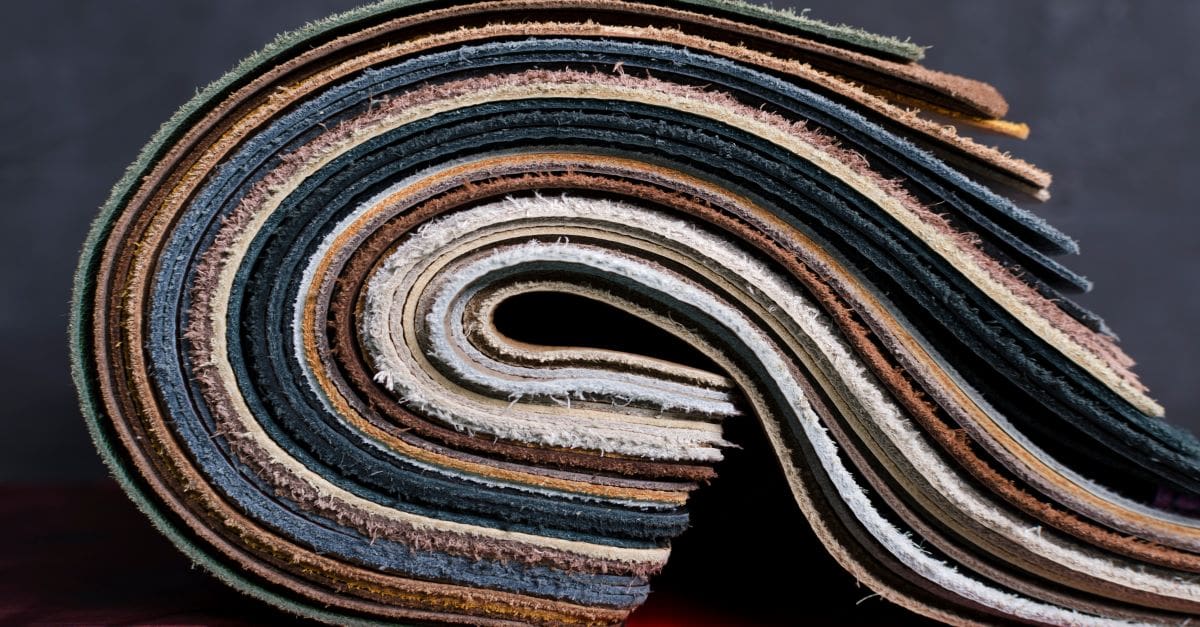
The New England area around Boston is known today for medical and biotechnology research and development, overtaking the dominance of the computer industry that flourished here for decades. In the mid-1800s, another industry — textiles — dominated the area with mills spotted throughout eastern Massachusetts and Rhode Island. Today, if you drive along route I-495, you’ll find many brick textile mills still standing but reimagined as office spaces and housing.
Just as the textile mills have expanded beyond their original purposes; the industry they served has expanded to new uses, including1
- Transport textiles;
- Medical and hygiene textiles;
- Industrial products and components;
- Agriculture, horticulture, and fishing;
- Home textiles;
- Clothing components;
- Packaging and containment;
- Construction materials;
- Geotextiles for civil engineering;
- Sports and leisure materials;
- Protective and safety materials; and
- Textiles for ecological protection.
Many of these applications are considered high-technology products made from woven, non-woven, and knitted materials made composed of natural and synthetic solid materials, as well as hollow fibers that offer increased thermal insulation. Other specialized products are essential to military and first responders since they protect against hazardous materials, biological components (particularly useful in today’s markets to protect against respiratory diseases), and injury from ballistic sources, cuts, fires, and explosions.
All three industries noted earlier (biotechnology, computers, and textiles) have depended upon the most advanced technologies of their day to ensure the production of high-quality products that would meet the requirements of their intended applications. In fabrics, that means automated production technologies, advanced testing to help ensure product quality, and informatics systems to manage lab operations, as well as data and information collection, organization, and utilization.
The role of laboratory testing
Laboratory testing is essential to the textile industry. For example, a textile lab is responsible for evaluating incoming raw materials to ensure they are fit for purpose. The industry understands that quality products depend on high-quality raw materials. Laboratories — usually quality control (QC) labs — will work with shipping and receiving departments to check the quality of incoming raw materials and ensure they meet the specifications for the products in production. Non-conforming materials will be rejected, and those that pass the testing will be moved into the production area.
Textiles labs are essential in other ways too. These labs are integrated into the production workflow for monitoring purposes, including both inline and test sample evaluation during the production process. Inline testing is non-destructive, whereas lab testing is intentionally destructive. This type of production monitoring testing aims to detect deviations from expected conditions and avoid the production of out-of-specification (OOS) materials. These labs may also conduct final product evaluation, which is a more thorough evaluation of the product to determine if it meets the requirements for a shippable material.
Beyond those activities, the laboratory’s testing capability can also be used to investigate customer satisfaction problems and cases where a product failed prematurely or is OOS.
Laboratory testing can also support research and development activities. In larger organizations, this and the resolution of customer satisfaction issues would be in a separate facility to avoid disrupting the QC operations. Still, smaller companies with fewer resources may use the QC lab for this work.
Test methods and accreditation
The testing methods consist of both chemical and physical testing. Chemical testing ensures that material is free from substances that may cause harm when placed in contact with a human or animal. These include harmful dyes, phthalates, heavy metals, and other substances that might remain from the production process. Color fastness and flammability are also important tests depending on the application for which the material is intended for.2 Optical inspection of materials is also used. For example, a microscopic analysis would determine the materials the product is made from.
Physical/mechanical tests such as tensile testing, abrasion testing, and pilling are also necessary. In addition, tests may be run to determine how weatherproof the material is to water vapor resistance and permeability.
The test methods themselves are standardized to ensure valid comparisons between producer and customer laboratories and come from a variety of sources, including ASTM International, the International Organization for Standardization (ISO), the American Association of Textile Chemists and Colorists (AATCC). Government requirements from the US Code of Federal Regulations, the Consumer Product Safety Improvement Act; and various Canadian and Chinese regulations also drive method standardization.
Laboratories doing textile testing are generally required to be accredited according to ISO 17025 specifications.
The role of informatics in textile manufacturing
Laboratory-generated data and information are critical to the successful operation of manufacturing and production processes. In order to gain full value from those elements, labs must be able to organize, analyze, and communicate test results to management, process control, and shipping and receiving, and in some cases where customer relationships are critical, the sales force may also have to resolve customer satisfaction issues.
Given a modern production operation, we can expect multiple products to be in production at any given time, each with its own testing requirements and raw materials inventory that has to be tested and approved or rejected. A laboratory informatics solution like a laboratory information management system (LIMS) system can relieve stress in the lab work environment by simultaneously managing multiple test suites for different products.
A LIMS has three sets of functions that help support laboratory testing:
- Workflow management – What work is coming in? What has to be done? What are the priorities? What results have to be approved and released? These are routine questions that occur in any production operation and testing labs are a prime example. These and related questions to lab operations are addressed by a LIMS. As part of its operations management samples can be logged in at the lab or remotely (and then identified as “in the lab” when they arrive). This makes it easier to keep track of work that is coming in and plan each day’s testing schedules.
- Results management and data logging/capture – LIMS provides a complete database for capturing and organizing samples and test results. Results can be entered manually, or for more efficiency via electronic data/information transfer from instruments and instrument data systems (IDSs). Most major IDSs have programming interfaces that permit downloading of work that has to be done through the IDS, and then upon completion permit sending the sample IDs and results back to the LIMS. This avoids manual data entry, greatly improves productivity, and provides a basis for 24/7 operations.
- Regulatory support – This is an important aspect of a LIMS’ capabilities. It provides traceability for data; if results are challenged, the lab can respond to it by looking at the data history (including audit trails), who carried out the analysis, and who approved the results. The lab can also see what equipment was used and verify its readiness for use. This also becomes important when you have to resolve customer questions about product characteristics.
The LIMS database can make it easier to organize and search product test data. It can be searched by product type, lot, or any other production criteria that have been entered into the sample description. You can also use it for statistical process control to look at trends in test results and answer questions about incoming raw materials, for example: “Are the product characteristics from a particular vendor stable or trending in one direction or another?”
In closing…
Textile manufacturing is a sophisticated production environment that depends heavily on laboratory testing to both monitor production and help ensure product quality. That requires fast access to information and the ability to search and generate reports that are meaningful to management and production personnel, as well as customer support specialists if required. Through its workflow management, results management, audit trail, and regulatory support functionality, a LIMS system can provide the support textile companies need to streamline lab operations and make it easier to produce, manage, access, and utilize lab data and information while reducing labor costs.
To read more about informatics in manufacturing, check out “LIMS in Manufacturing” in the LabLynx library.
To learn more about the LabLynx ELab LIMS for the Manufacturing Industry, contact sales@lablynx.com or visit www.lablynx.com.
References
1 https://textiletutorials.com/12-applications-of-technical-textiles-12-types-of-technical-textiles/
2 https://humiditycontrol.com/what-is-textile-testing/
Accelerate Your Lab's Success & Experience LabLynx
"*" indicates required fields
Explore the LabLynx Suites
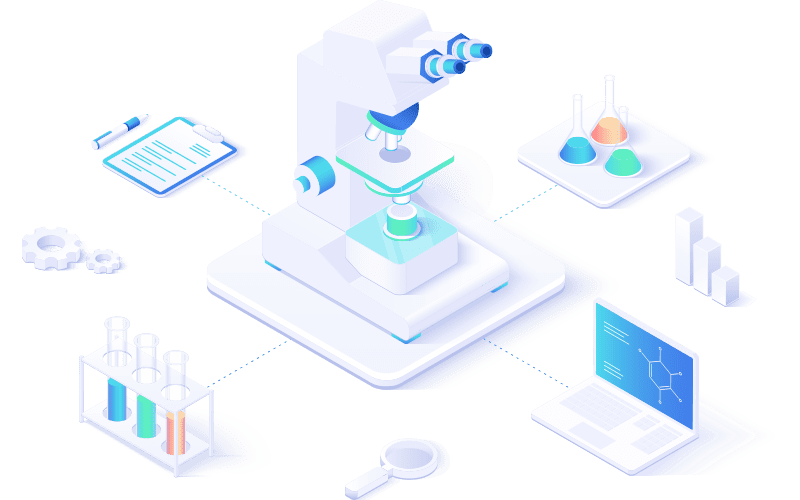
LIMS Suite
Seamless Sample and Workflow Management
The LabLynx LIMS Suite empowers laboratories with the tools needed to manage samples, workflows, compliance, and more in one centralized system. It’s the backbone for labs seeking efficient, reliable, and scalable management solutions.
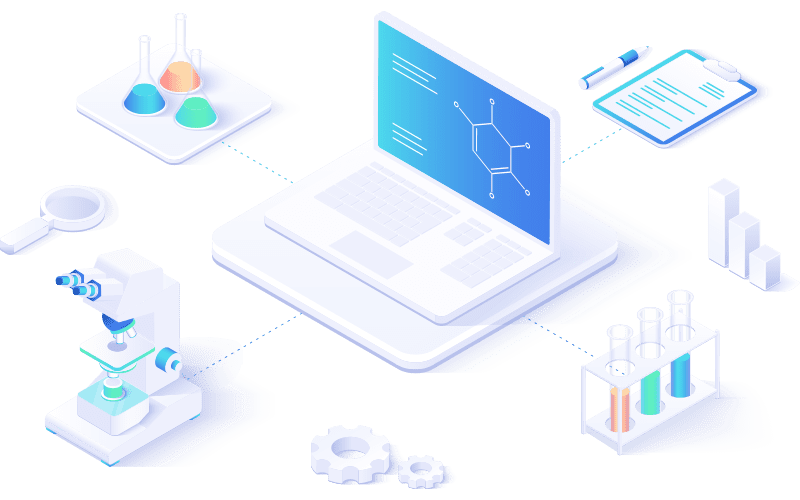
ELN Suite
The LabLynx ELN Suite offers a modern approach to managing lab data and experiments. With its secure, intuitive platform, your team can record, store, and collaborate effortlessly, supporting innovation every step of the way.
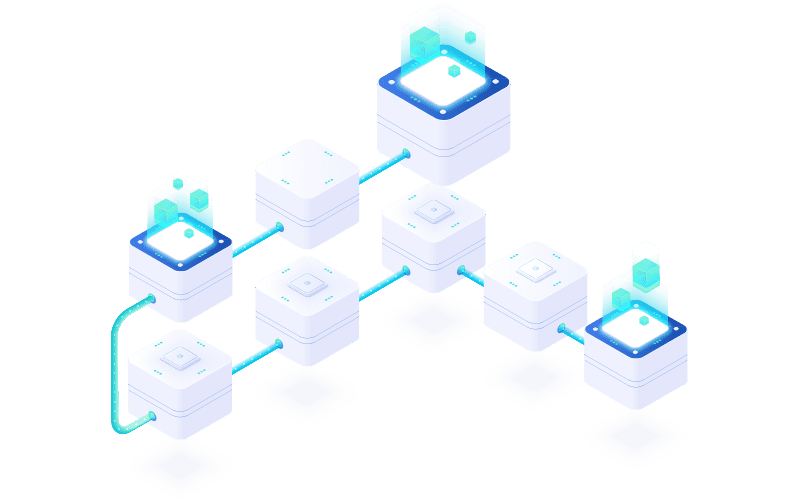
Lab Automation
Automate for Efficiency and Growth
Streamline operations and boost productivity with the LabLynx Lab Automation Suite. Designed for labs ready to embrace advanced automation, this suite integrates systems, instruments, and workflows to deliver efficiency at scale.